While patient safety has always been the predominate consideration in healthcare delivery, the pandemic prompted the industry to renew its focus on safety and highlighted opportunities to innovate around improving patient well-being across all stages of care delivery.
As healthcare design specialists, we recognize the importance of designing environments of care that include innovative solutions to enhance safety for patients, providers, and community members alike. Opportunities can be found throughout the design process. Facility planning, design, product specification, and cleaning and maintenance requirements all present opportunities to focus on enhancing safety and preventing or mitigating the spread of infectious diseases.
Innovative Solutions for Antivirus Design
Now more than ever, healthcare facility planning and design experts are challenged with designing to maximize opportunities for distancing, manage patient-flow effectively, and increase control over the spread of germs and infection. To adapt, planning solutions are focusing more and more on a few key areas:
- Mechanical: HVAC and space modifications can accommodate better air quality and flow.
- Technology: Telemedicine and teleworking are part of daily conversations in the healthcare world now. Touchless automation is also becoming very common. Consider public restrooms and staff lounges. They are highly trafficked areas. To minimize or avoid contact with surfaces, these areas can be designed with door-free entrances and touchless fixtures.
- Behavior-based solutions: Organizing human behaviors and activities around best practices can minimize the spread of germs. For example, identifying opportunities that encourage handwashing and sanitizing is common in planning conversations.
- Space assessment: Environments are shifting from a focus on large areas for groups to individual spaces that promote social distancing. In turn, designers are challenging themselves to rethink floor plans and occupancy preferences. The square footage, shape, location, and furniture in waiting rooms need more flexibility. There is a growing assumption that greater quantities of smaller healthcare spaces could replace those that are larger.
Considering these observations, designs will need to adapt to best foster patient safety and confidence. For example, consider the use of radio frequency identification (RFID). Increasing its use in a space can help locate and notify patients, and also provide opportunities for a more hygienic environment.
When specifying products, identifying appropriate products from a multi-attribute perspective and making evidence-based decisions are incredibly important in the COVID-19 era. Consider:
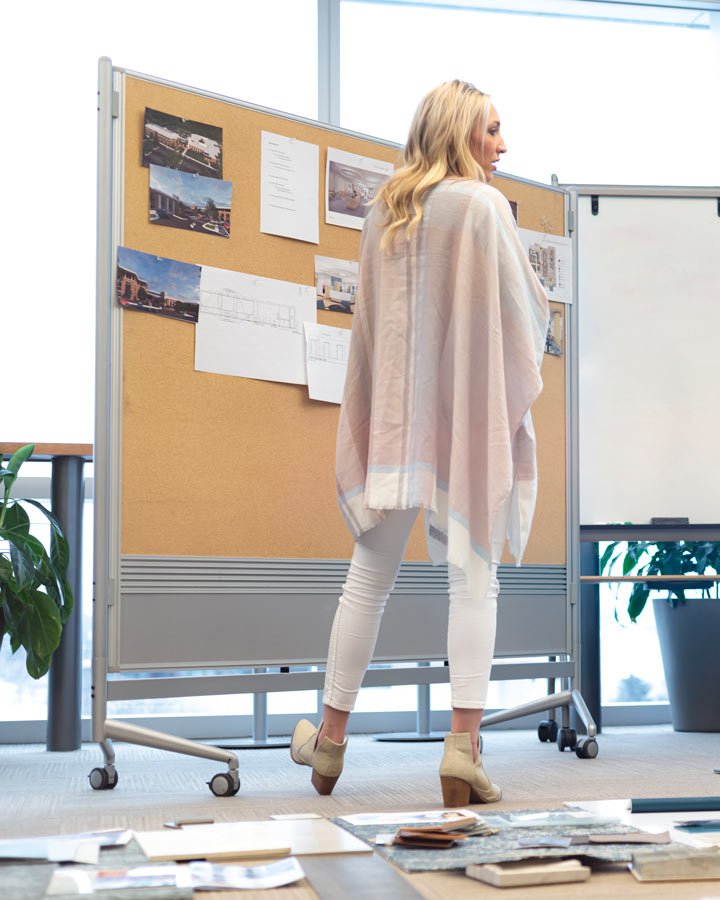
- Durability: Durable products that can be easily and effectively sanitized are invaluable in the design of antivirus environments. Whether it be a floor or wall finish, a work surface or a piece of furniture, having cleanable and long-lasting products plays a major role people’s health within healthcare facilities.
- Performance-based qualities: This avoids premature product failures. Consider work surfaces and casework. They should be smooth and free from crevasses and gaps, helping minimize areas where germs can get trapped. Additionally, seams should have finishes that can withstand the heavy use of chemical cleaners. This will help products have longer shelf lives.
- Imperviousness and shape: Solid surfaces such as laminate with high-performance finishes, quartz, stainless steel, or copper are great options. The shape of materials in their final form is also worth noting. Specifically, flat surfaces are where germs can sit and accumulate over time. By reducing the number of flat surfaces and incorporating rounded edges into a design, you can help minimize instances where people encounter germs.
- New technology: As innovations and new technologies continue to develop, they play valuable roles in an antivirus interior design. Paint and UV technology are examples. Such products offer significant improvements in cleaning cycle times, as well as offer reductions in pathogens. For example, as explained in the whitepaper “Smart Just Got Smarter” from Providence St. Peter, an operating room cycle time can be reduced by nearly 60 percent, from 25 minutes to 10 minutes. In assessing cycle times, it should be noted that they can vary as designs differ from room to room. For example, some surfaces may not be painted (e.g., cabinets, equipment, windows, glass walls). Floor colors and finishes can also have an impact.
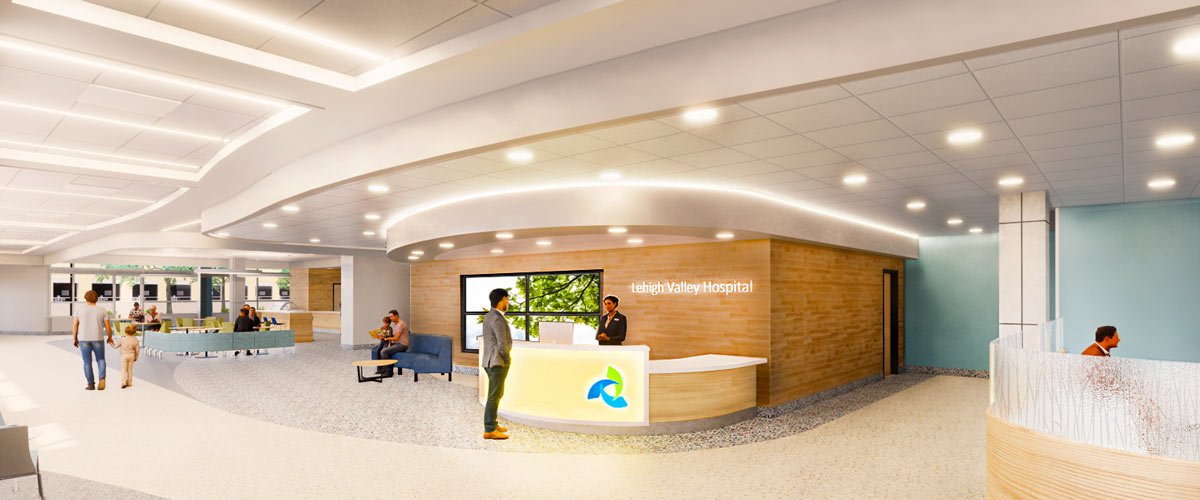
USING INNOVATIVE TECHNOLOGY
ERDMAN has firsthand experience with how innovative technology can play a role in virus-resistant designs. Through our work with Lehigh Valley Health Network, LVHN has begun using UV disinfection technology with the use of Tru-D, which is a device that calculates the precise dose of UV-C light needed to kill up to 99.99 percent of harmful pathogens. Reflective paint is also being proposed for LVHN, including Lumacept and SMARTfinish.
- Furniture: Removable parts such as wipe-out seats and replaceable cushions will be vital to allow for the ease of cleaning and flexibility. Fabrics must be crock and flame resistant, as well as strong enough to withstand being torn and stretched. Antimicrobial technology should also be considered when specifying furniture to help minimize or stop the growth of germs.
- Age of existing finishes: Replace worn and stained items, whether they are finishes, furniture, or accessories at a diligent pace. Old, distressed surfaces are breeding grounds for bacteria. In turn, the cost associated with fabric failures in healthcare can be staggering. To that end, a new group in the industry has been formed. It is called the Durable Coated Fabrics Task Force, and consists of industry professionals, chemists, and technical representatives. As part of this task force, a toolkit has been developed to inform designers of best practices to follow in their product specifications. Fabric selection guides and minimum standards are outlined.
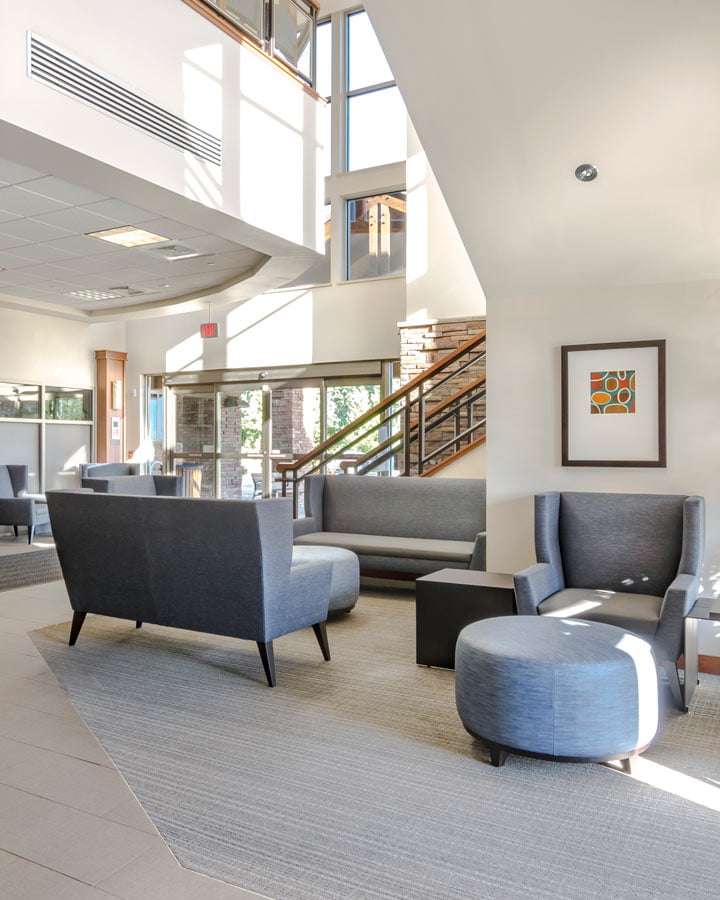
What is the Durable Coated Fabrics Task Force?
The Durable Coated Fabrics Task Force is an interdisciplinary group of experts and professionals. Its members educate stakeholders and address performance parameters of durable coated fabrics in acute, ambulatory, and long-term care settings. The group is comprised of the following organizations:
- American Academy of Healthcare Interior Designers (AAHID)
- Healthcare Designers (inhouse to healthcare systems)
- Healthcare Designers (firmed based)
- EVS (Environmental Services) – Cleaning/Disinfection Experts
- BIFMA (Business and Institutional Furniture Manufacturers Association)
- CFFA (Chemical Fabrics and Film Association)
- VI (The Vinyl Institute)
- Chemists/Technical Representatives
- Manufacturers/Distributors of Durable Coated Fabrics
Cleaning vs. Sanitizing vs. Disinfecting
CLEANING
- Removes material like dust, soil, blood, and body fluid
- Physically removes rather than kills microorganisms (which can be done with water, detergents, and mechanical action)
- Is always essential prior to disinfection or sterilization
- Is needed as a surface that has not been cleaned effectively cannot be properly disinfected or sterilized
Sanitizing
- Has a general claim of germ control, but generally not organism specific
- There are two basic kinds of sanitizers:
- Food contact surfaces 99.999% (a 5-log reduction)
- Nonfood contact a reduction of 99.9% (3 logs) within 30 seconds
Disinfecting
- Inactivates pathogens
- Usually involves chemicals, heat or UV
- Destroys microbial life including bacteria, viruses, spores, and fungi
- Is commonly used as quaternary ammonium compound products, hydrogen-based products, and sodium hypochlorite (bleach)
ERDMAN Takeaway
Safety is paramount. As design professionals, we can equip ourselves and our clients with the knowledge and information necessary to design facilities that increase patient safety in a post-pandemic era. We must be flexible in designing for the future, and work alongside our healthcare partners to shape facilities that are both safe and efficient.
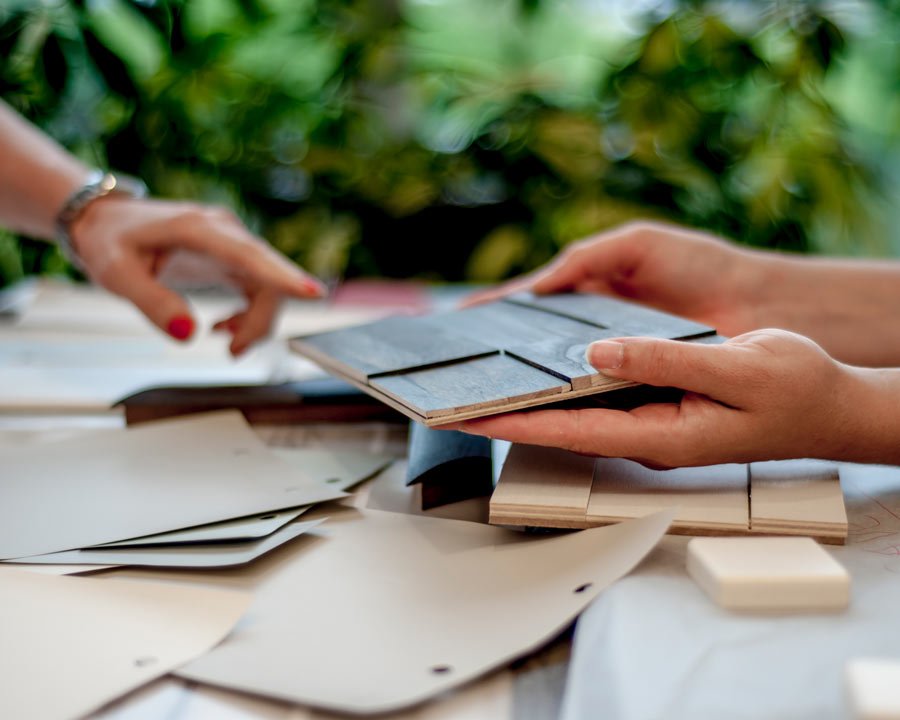
Strategic planning and design, informed product specifications, and superior cleaning and maintenance routines all contribute to a building’s health status.
If you are looking to document the health of your building, this can be achieved through an existing initiative like the WELL Building Standard®. This is a performance-based system for measuring, certifying, and monitoring building features that impact human health and wellbeing. A guide like this will give building users more confidence in their interior environments. The good news is that even without the official certification, smart design tactics like those described above can decrease the rate of sickness, alleviate symptoms of illness, and improve mental functions, outlook, and mood. COVID-19 has not changed this, but rather heightened the need to design healthier facilities.
- ASHE. (2020) COVID-19 Recovery. https://www.ashe.org/covid-19-recovery?utm_source=HFM%20Insider%20%28weekly%20e%2Dnewsletter%29&utm_medium=email&utm_campaign=HFM%20Insider%3A%205%2F19%2F20
- DCF Task Force (n.d.). What is a Durable Coated Fabric?https://www.durablecoatedfabrics.com/#:~:text=The%20Durable%20Coated%20Fabrics%20Initiative,and%20Terry%20 Murphy%20from%20The
- Dickson, A., Nicodemus, R., Roundy, J., & Staubitz, L. (2020, January 15). Tru-D Success Story: Providence St. Peter Hospital; Olympia, Washington. Tru-D Smart UVC. https://www.slideshare.net/CampbellKane/trud-smartuvc-success-story
- Fuglsang, M. (n.d.). Know Your Surface. Infection Control Today. https://www.infectioncontroltoday.com/view/know-your-surface 5. Harris, D., Rohde, J., & Solomon, S. Surfaces, Materials, and Disinfection: COVID-19 and Beyond [PowerPoint slides]. https://static1.squarespace.com/static/5c48b8275417fcea6c40bd89/t/5ec43f277fbe9e0dd8a329c4/1589919546298/IntVwWbnr_PPT_Interior+Surfaces_v5_5_11_2020_Harris_Solomon_Rohde_REVIEWED_FINAL.pdf
- International WELL Building Institute. (n.d.). Explore the Standard. https://www.wellcertified.com/certification/v1/standard/