Scope reprocessing areas are very plumbing-intensive and require considerable design planning.
Scope reprocessing areas in digestive health centers are dedicated to the cleaning, disinfection and drying of scopes used in imaging the digestive tract. They are very plumbing-intensive and can be daunting even for those familiar with them.
In my previous piece (November 2021) in this two-part series, I discussed standard staff workflows in these areas, common medical equipment and fixtures, and typical plumbing systems needed. In Part 2, I will take you through design guidance for the systems discussed in Part 1 and other important considerations when dealing with these areas.
While there are many different design choices and considerations for scope reprocessing areas, some of the more critical ones warrant mention here.
Discovery in Remodeled Areas
While designing scope reprocessing areas is intensive on its own, remodeling existing areas for new equipment adds another layer of complexity. Digestive health centers that are making reprocessing equipment upgrades may not have adequate capacity or even infrastructure in several plumbing systems, and it is important to survey these early. Depending on the scope, some systems may need upgrades to source equipment or entire refits.
Compressed air is a likely system to need improvements in a remodel, especially as facilities migrate from scope drying racks to drying cabinets needing generous amounts of high-quality air. Existing facilities often do not have compressed air of a quality or quantity for this equipment. Drying cabinets are often the driver for the selection of compressed air equipment and pipe size. Other equipment tends to add a much smaller load and can use the same quality air, even if not required.
Purified water is another system deserving close study during discovery. Some existing reprocessing areas use purified water already, but others may only have softened or even tap water. Scope reprocessors usually prefer some level of reverse osmosis water, but many can handle softened or even tap water in a pinch. Not all facilities use a purified water faucet at their decontamination sinks, but many will if given the opportunity, so it is always worth asking the users.
As with all remodels, correctly locating floor penetrations and understanding their impact on the structure is paramount. Floor sinks for scope reprocessors can present the biggest challenge for this, as they must be located in a target area specified by the manufacturer, as shown in Figure 1.
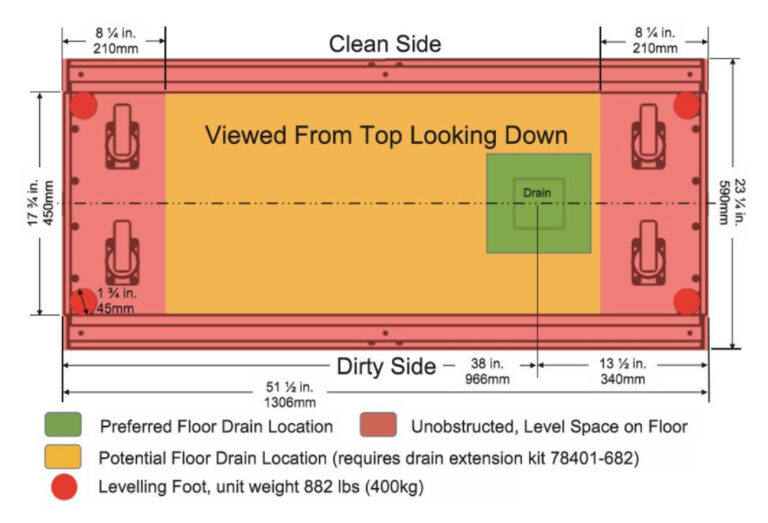
While square floor sinks often provide a larger target for the reprocessor drain, they can be more disruptive to rebar and other floor structures due to their footprint and need for slab overcuts. Round floor sinks can be a better option since core drilling reduces these risks. In either case, it is always a good idea to get an x-ray map of the rebar and review it with a structural engineer before settling on a final location.
System Selection
As discussed in Part 1 of this series, scope reprocessing areas require many different plumbing systems; each of them should be tailored to the requirements of the equipment and staff. In addition to being plumbing-intensive, they are also labor-intensive for those staffing them. It is not uncommon for all equipment to be running at once. Areas often operate near peak capacity most of the day to keep up with caseloads as well.
With this in mind, it is important to design the systems serving it with little to no diversity. Equally important, systems should be designed so that no single point of failure is in any of them, as a failure would bring procedures and the revenue they generate to a halt.
Domestic water and sanitary waste and vent systems for these areas are fairly straightforward, as their required capacities can be determined through equipment flow rates and fixture unit methods according to plumbing codes. The decontamination sinks generally determine the domestic hot water temperature to supply to the area; they are not subject to code-mandated handwashing temperatures.
Staff are trained to deal with water hotter than this, but they should still be asked what they prefer for a maximum temperature. Scope reprocessors will require lower temperature water tempered through thermostatic mixing valves. Supplying each unit with its own mixing valve is a good idea in the interest of not having a single point of failure.
Not all facilities use purified water in reprocessing. Unless the scope reprocessors require it, you should ask the client if they intend to use purified water. If they do, they will often want it piped to dedicated faucets at the decontamination sinks as well as the reprocessors. The reprocessors will drive the purified water quality, and while some are vague on specifics, ASTM Type III water, per the characteristics in Figure 2, is usually acceptable.
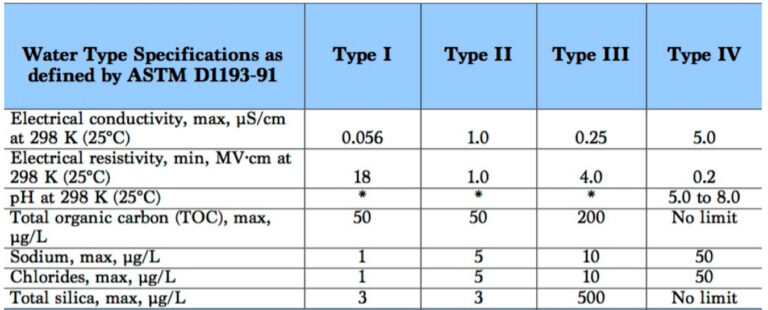
While purified water is preferred, many reprocessors do not require it and can instead handle 10 grains/gallon maximum hardness, but you should always consult the manufacturer to confirm.
Compressed air quality is likely to be determined by the drying cabinets, but the reprocessors and air guns at the sinks can be connected to the same system. ISO 8573-1 Class 0 air per the characteristics below is very common.
It is important to note that Class 0 is of higher quality than Class 1, but the requirements are specified by the equipment and not the ISO standard. These equipment specifications will ultimately determine the fineness of oil and particulate filters needed on the source equipment. Desiccant dryers also are needed to meet the dew point requirement.
Air compressors, dryers and filters should also be chosen with N+1 redundancy to allow for operation during maintenance and to eliminate a single point of failure.
Piping and Layout
While much of the piping to reprocessing areas will be kept concealed above the ceiling, there are some exceptions to this. Reprocessors require a series of prefilters, along with a backflow preventer and mixing valve, and occasionally a pressure-reducing valve, on their water supply, as shown in Figure 3.
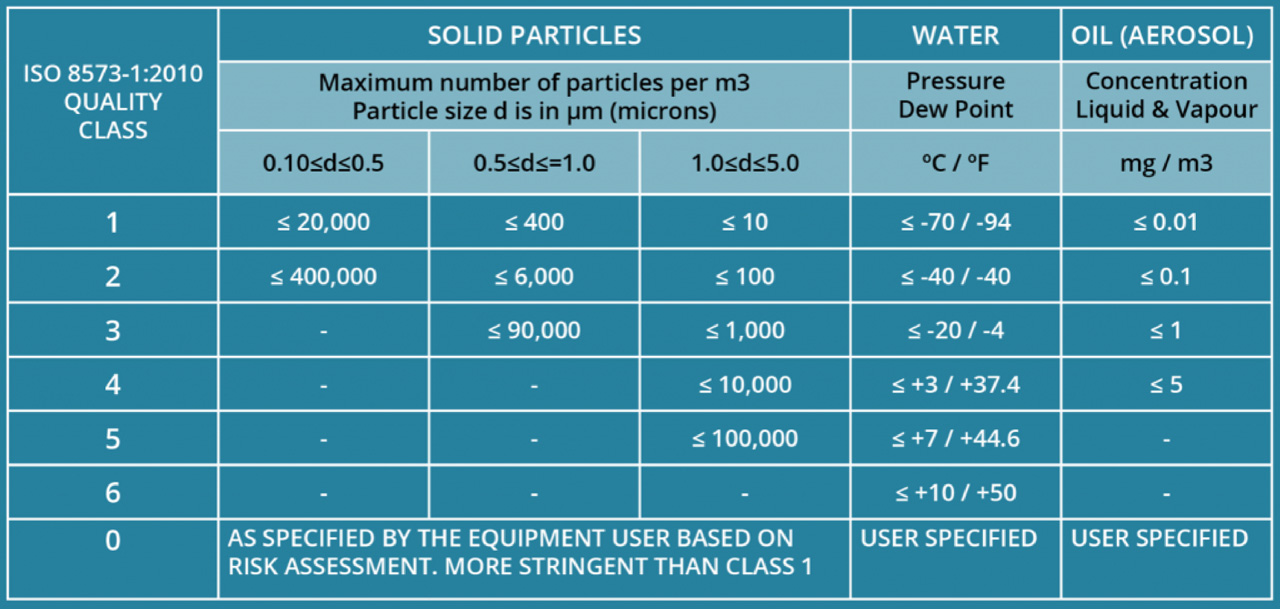
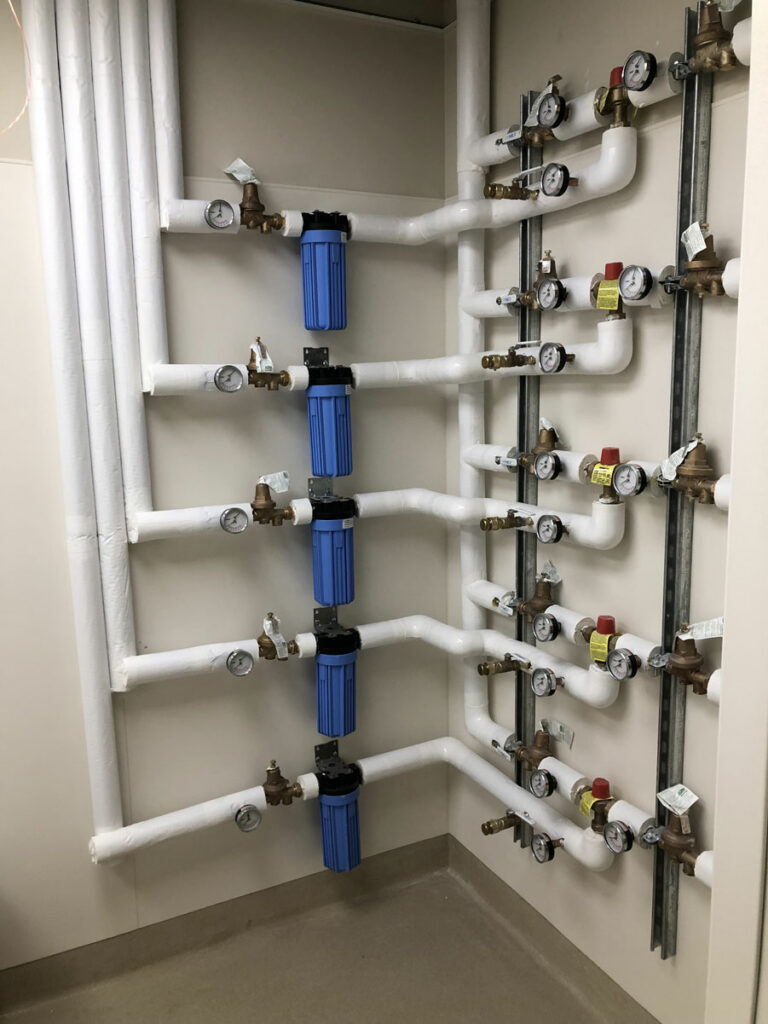
All these need to be kept accessible for testing, maintenance and adjustment; dedicated wall space also is needed to mount them. They can either be kept exposed or concealed in a cabinet; in either case, they should be kept on the dirty side of the area. Circulated domestic hot water mains should be kept close to these assemblies, as reprocessors have stringent temperature tolerances. Each reprocessor should have its own isolation valves for water and air; some manufacturers recommend access panels for these, as shown in Figure 4.
Backflow preventers are necessary on the reprocessors and, occasionally, the decontamination sinks. Reprocessors are high health-hazard devices; their internal pumps can create backpressure, so a reduced-pressure principle assembly (ASSE 1013) is required. If a sink faucet has a self-closing sprayer that could submerge in the basin, its supply lines should be equipped with spill-resistant pressure vacuum breakers (ASSE 1056).
As with water supplies, compressed air supplies to equipment should be given individual isolation valves. Drying cabinets and reprocessors generally accept air pressures as generated by a typical compressor (up to 140 psi or so), but air guns should be regulated down to 30 psi at each sink. To eliminate single points of failure and promote ease of maintenance, source equipment is best configured in a setup similar to Figure 5.
Emergency Fixtures
As scope reprocessing areas deal with biohazardous waste and chemical cleaners coupled with splashing water and compressed air, they require emergency eye and face wash fixtures. An emergency fixture should be placed on both the dirty and clean sides.
To meet OSHA requirements, fixtures and their placement should be selected in accordance with ANSI Z358.1.
Scope reprocessing areas are very plumbing-intensive and require considerable design planning. Plumbing engineers should get involved as early as possible to understand equipment requirements, staff workflows, needed source equipment and space considerations.
As the U.S. population ages and the need for digestive health centers rise, those involved in health-care design should expect to see more of these projects.
For additional information, visit these websites:
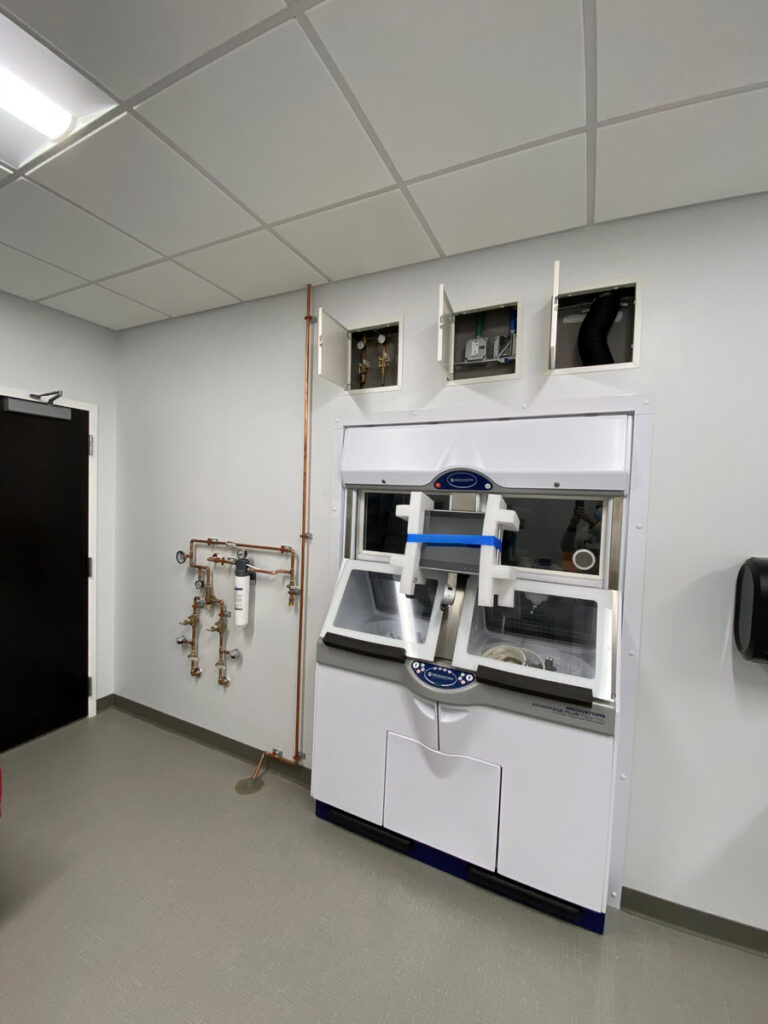
Aaron Bock, PE, CPD, GPD, LEED AP, EDAC, is a senior plumbing engineer at ERDMAN, and past president of the Wisconsin chapter of the American Society of Plumbing Engineers. He has been designing plumbing and medical gas systems for the health-care industry since 2007, with a specific interest in waterborne bacterial control. Bock has completed more than 250 projects across the United States and is a graduate of the University of Wisconsin-Madison and ERDMAN’s INSPIRE leadership program.
Original article published by PHCP PROS